Destylarka do rozpuszczalników
Destylarka do rozpuszczalników to urządzenie, które ma wiele zalet, szczególnie w kontekście przemysłowym i laboratoryjnym. Przede wszystkim umożliwia efektywne oddzielanie różnych substancji chemicznych poprzez wykorzystanie różnicy w temperaturze wrzenia. Dzięki temu procesowi można uzyskać czystsze produkty, co jest kluczowe w wielu zastosowaniach, takich jak produkcja farb, lakierów czy rozpuszczalników organicznych. Kolejną istotną zaletą jest oszczędność kosztów. Inwestycja w destylarkę pozwala na odzyskiwanie rozpuszczalników, co zmniejsza wydatki na ich zakup oraz ogranicza ilość odpadów chemicznych, które muszą być utylizowane. Dodatkowo, nowoczesne destylarki często są wyposażone w zaawansowane systemy filtracji oraz automatyzacji, co zwiększa ich wydajność i ułatwia obsługę. Użytkownicy mogą również liczyć na poprawę bezpieczeństwa pracy, gdyż zamknięte systemy destylacyjne minimalizują ryzyko uwolnienia szkodliwych oparów do atmosfery.
Jakie rodzaje destylarek do rozpuszczalników są dostępne
Na rynku dostępnych jest wiele rodzajów destylarek do rozpuszczalników, co pozwala na ich szerokie zastosowanie w różnych branżach. Najpopularniejsze z nich to destylarki prostokątne oraz cylindryczne, które różnią się kształtem i sposobem działania. Destylarki prostokątne charakteryzują się większą powierzchnią wymiany ciepła, co przekłada się na wyższą efektywność procesu destylacji. Z kolei destylarki cylindryczne są bardziej kompaktowe i łatwiejsze w obsłudze, co czyni je idealnym rozwiązaniem dla mniejszych laboratoriów. Innym istotnym podziałem jest klasyfikacja według sposobu chłodzenia. Można wyróżnić destylarki z chłodzeniem wodnym oraz powietrznym. Te pierwsze zapewniają lepszą efektywność chłodzenia, co jest ważne przy pracy z substancjami o wysokiej temperaturze wrzenia. Warto również zwrócić uwagę na destylarki próżniowe, które umożliwiają przeprowadzanie procesów w obniżonym ciśnieniu. Dzięki temu można destylować substancje w niższych temperaturach, co jest korzystne dla termolabilnych związków chemicznych.
Jakie materiały są najczęściej używane w budowie destylarek
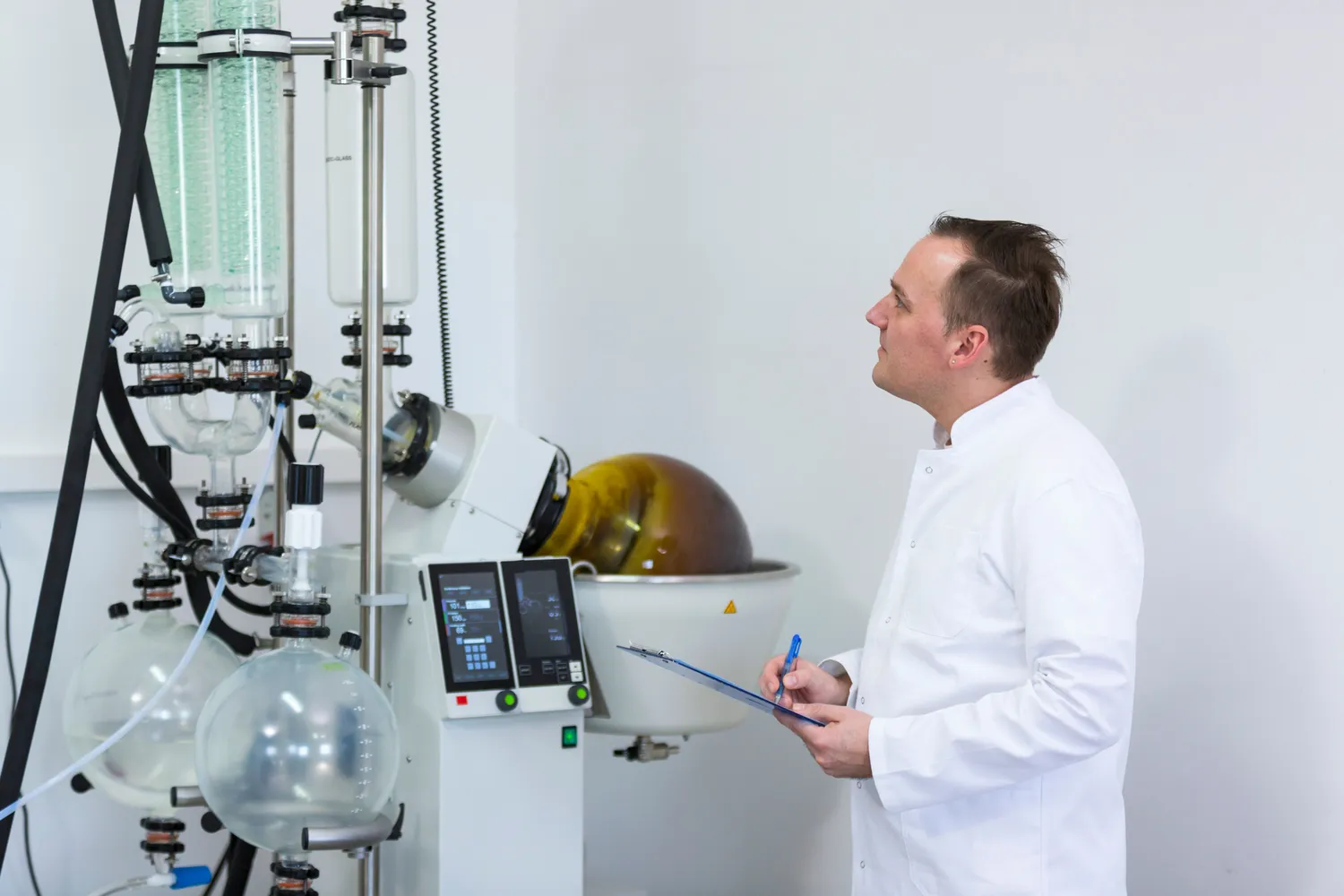
Budowa destylarek do rozpuszczalników opiera się na różnych materiałach, które muszą spełniać określone wymagania dotyczące odporności chemicznej oraz termicznej. Najczęściej stosowanym materiałem jest stal nierdzewna, która charakteryzuje się wysoką odpornością na korozję oraz trwałością. Stal nierdzewna jest idealna do kontaktu z wieloma substancjami chemicznymi i zapewnia długowieczność urządzenia. Innym popularnym materiałem jest szkło borokrzemowe, które jest stosowane głównie w mniejszych destylarkach laboratoryjnych. Szkło borokrzemowe ma doskonałe właściwości termiczne i chemiczne, a także umożliwia łatwe monitorowanie procesu destylacji dzięki przezroczystości materiału. W przypadku elementów grzewczych często wykorzystuje się materiały ceramiczne lub metalowe o wysokiej przewodności cieplnej. Ważnym aspektem jest również izolacja termiczna, która zapobiega utracie ciepła i zwiększa efektywność energetyczną całego systemu.
Jakie zastosowania mają destylarki do rozpuszczalników w przemyśle
Destylarki do rozpuszczalników znajdują szerokie zastosowanie w różnych gałęziach przemysłu ze względu na swoją wszechstronność i efektywność. W przemyśle chemicznym są wykorzystywane do oczyszczania surowców oraz odzyskiwania cennych substancji chemicznych z odpadów produkcyjnych. Proces ten pozwala nie tylko na oszczędności finansowe, ale także na zmniejszenie negatywnego wpływu na środowisko poprzez ograniczenie ilości odpadów chemicznych. W branży kosmetycznej destylarki służą do produkcji perfum oraz ekstraktów roślinnych, gdzie kluczowe jest uzyskanie wysokiej czystości składników aktywnych. Również przemysł farmaceutyczny korzysta z tych urządzeń do produkcji leków oraz substancji czynnych, gdzie precyzyjne oddzielanie składników ma ogromne znaczenie dla jakości końcowego produktu. Ponadto destylarki są wykorzystywane w laboratoriach badawczych do analizy substancji chemicznych oraz opracowywania nowych metod syntez chemicznych.
Jakie są najczęstsze problemy z destylarkami do rozpuszczalników
Podczas użytkowania destylarek do rozpuszczalników mogą wystąpić różne problemy, które mogą wpływać na efektywność ich działania oraz jakość uzyskiwanych produktów. Jednym z najczęstszych problemów jest zatykanie się elementów filtracyjnych, co może prowadzić do obniżenia wydajności destylacji. Zatykanie może być spowodowane obecnością zanieczyszczeń w surowcach lub niewłaściwym doborem materiałów filtracyjnych. W takich przypadkach konieczne jest regularne czyszczenie lub wymiana filtrów, aby zapewnić prawidłowe działanie urządzenia. Innym istotnym problemem jest niewłaściwe ustawienie temperatury grzania, co może prowadzić do nieefektywnego oddzielania substancji. Zbyt niska temperatura może uniemożliwić destylację, podczas gdy zbyt wysoka może prowadzić do degradacji termicznej cennych składników. Użytkownicy powinni również zwracać uwagę na szczelność systemu, ponieważ nieszczelności mogą powodować utratę oparów i zmniejszenie efektywności procesu. W przypadku destylarek próżniowych istotne jest monitorowanie poziomu próżni, ponieważ jego spadek może wpłynąć na jakość destylatu.
Jakie są koszty związane z zakupem destylarki do rozpuszczalników
Koszty zakupu destylarki do rozpuszczalników mogą się znacznie różnić w zależności od wielu czynników, takich jak typ urządzenia, jego pojemność oraz dodatkowe funkcje. Na rynku dostępne są zarówno małe destylarki laboratoryjne, które mogą kosztować od kilku tysięcy złotych, jak i duże przemysłowe systemy destylacyjne, których cena może sięgać setek tysięcy złotych. Warto również uwzględnić koszty eksploatacji, które obejmują zużycie energii elektrycznej, koszty materiałów eksploatacyjnych oraz konserwacji. W przypadku dużych instalacji przemysłowych istotnym elementem są także koszty związane z przestrzenią roboczą oraz infrastrukturą potrzebną do ich prawidłowego funkcjonowania. Dodatkowo warto rozważyć inwestycję w nowoczesne technologie automatyzacji, które mogą zwiększyć wydajność procesu, ale również podnieść całkowity koszt zakupu. Przy wyborze odpowiedniej destylarki warto przeanalizować nie tylko cenę zakupu, ale także potencjalne oszczędności wynikające z odzyskiwania rozpuszczalników oraz poprawy jakości produkcji.
Jakie są wymagania dotyczące bezpieczeństwa przy używaniu destylarek
Bezpieczeństwo użytkowania destylarek do rozpuszczalników jest kluczowym aspektem, który należy uwzględnić podczas ich eksploatacji. Przede wszystkim ważne jest przestrzeganie zasad BHP oraz stosowanie odpowiednich środków ochrony osobistej, takich jak rękawice ochronne, gogle czy maski przeciwgazowe, szczególnie w przypadku pracy z substancjami chemicznymi o wysokiej toksyczności. Użytkownicy powinni być świadomi ryzyka związanego z wybuchem oparów rozpuszczalników, dlatego istotne jest zapewnienie odpowiedniej wentylacji w pomieszczeniu roboczym oraz unikanie źródeł zapłonu w pobliżu urządzenia. Dodatkowo ważne jest regularne sprawdzanie stanu technicznego destylarki oraz jej elementów składowych, aby uniknąć nieszczelności czy uszkodzeń mogących prowadzić do wycieku substancji chemicznych. W przypadku pracy z dużymi ilościami rozpuszczalników warto również rozważyć zastosowanie systemów detekcji gazów oraz automatycznych systemów gaśniczych, które mogą znacząco zwiększyć poziom bezpieczeństwa w miejscu pracy.
Jakie innowacje technologiczne dotyczą destylarek do rozpuszczalników
W ostatnich latach na rynku destylarek do rozpuszczalników można zauważyć wiele innowacji technologicznych, które mają na celu zwiększenie efektywności procesów oraz poprawę jakości uzyskiwanych produktów. Jednym z najważniejszych trendów jest automatyzacja procesów destylacyjnych, która pozwala na precyzyjne kontrolowanie parametrów pracy urządzenia, takich jak temperatura czy ciśnienie. Dzięki zastosowaniu nowoczesnych systemów sterowania możliwe jest osiągnięcie większej powtarzalności wyników oraz minimalizacja błędów ludzkich. Kolejnym istotnym kierunkiem rozwoju są technologie odzyskiwania ciepła, które pozwalają na wykorzystanie energii cieplnej generowanej podczas procesu destylacji do podgrzewania surowców lub innych mediów roboczych. Takie rozwiązania przyczyniają się do zmniejszenia kosztów eksploatacyjnych oraz poprawy efektywności energetycznej całego systemu. Innowacje obejmują również rozwój materiałów o lepszej odporności chemicznej i termicznej, co przekłada się na dłuższą żywotność urządzeń oraz ich większą niezawodność.
Jakie są różnice między destylarkami a innymi metodami oczyszczania
Destylarki do rozpuszczalników różnią się od innych metod oczyszczania substancji chemicznych pod względem zasad działania oraz efektywności w określonych zastosowaniach. Główna różnica polega na tym, że destylacja opiera się na różnicy temperatur wrzenia składników mieszaniny, co pozwala na ich skuteczne oddzielanie. Inne metody oczyszczania, takie jak ekstrakcja czy adsorpcja, działają na innych zasadach i mogą być mniej efektywne w przypadku substancji o podobnych temperaturach wrzenia. Destylacja jest szczególnie korzystna w sytuacjach, gdy konieczne jest uzyskanie wysokiej czystości produktu końcowego lub gdy zachodzi potrzeba odzyskiwania cennych rozpuszczalników z odpadów produkcyjnych. W porównaniu do metod mechanicznych czy chemicznych, procesy destylacyjne często wymagają mniejszych nakładów czasu i energii przy odpowiednim dostosowaniu parametrów pracy urządzenia.
Jakie są najlepsze praktyki dotyczące konserwacji destylarek
Aby zapewnić długotrwałą i efektywną pracę destylarek do rozpuszczalników, niezwykle ważne jest przestrzeganie najlepszych praktyk konserwacyjnych. Regularna konserwacja powinna obejmować dokładne czyszczenie wszystkich elementów urządzenia po zakończeniu cyklu produkcyjnego lub po każdym użyciu. Zanieczyszczenia mogą wpływać na jakość uzyskiwanego produktu oraz prowadzić do uszkodzeń mechanicznych komponentów systemu. Należy również regularnie sprawdzać stan uszczelek i połączeń rurkowych; wszelkie nieszczelności powinny być natychmiast naprawiane, aby uniknąć strat surowców i niebezpieczeństw związanych z wyciekami substancji chemicznych. Ważnym aspektem konserwacji jest kontrola systemu grzewczego; wszelkie nieprawidłowości powinny być zgłaszane technikom serwisowym celem szybkiej interwencji. Użytkownicy powinni również regularnie kalibrować urządzenie zgodnie z zaleceniami producenta; właściwe ustawienia parametrów pracy mają kluczowe znaczenie dla jakości procesu destylacji.