Destylacja rozpuszczalników
Destylacja rozpuszczalników to proces, który polega na oddzieleniu składników mieszaniny na podstawie różnic w ich temperaturach wrzenia. Jest to technika szeroko stosowana w chemii, przemyśle farmaceutycznym oraz w produkcji alkoholi. Proces ten zaczyna się od podgrzewania cieczy, co prowadzi do jej parowania. Gdy temperatura osiągnie punkt wrzenia jednego ze składników, para tego składnika unosi się do góry i przechodzi przez chłodnicę, gdzie skrapla się z powrotem do postaci cieczy. Kluczowym elementem tego procesu jest wybór odpowiedniego sprzętu, takiego jak kolumna destylacyjna, która zwiększa efektywność separacji poprzez wielokrotne skraplanie i parowanie. W praktyce destylacja może być przeprowadzana w różnych warunkach, takich jak destylacja prosta, frakcyjna czy też destylacja pod ciśnieniem.
Jakie są najczęstsze zastosowania destylacji rozpuszczalników
Destylacja rozpuszczalników znajduje szerokie zastosowanie w różnych dziedzinach przemysłu i nauki. W przemyśle chemicznym jest wykorzystywana do oczyszczania substancji chemicznych oraz do separacji składników z mieszanin. Na przykład, w produkcji alkoholi, takich jak whisky czy wino, destylacja jest kluczowym etapem, który pozwala uzyskać pożądany poziom czystości i mocy trunku. W laboratoriach chemicznych destylacja jest często stosowana do izolacji i oczyszczania reagentów oraz produktów reakcji chemicznych. Innym ważnym zastosowaniem jest recykling rozpuszczalników organicznych, gdzie proces ten pozwala na odzyskanie użytych substancji chemicznych, co przyczynia się do ochrony środowiska oraz redukcji kosztów produkcji.
Jakie są różnice między destylacją prostą a frakcyjną
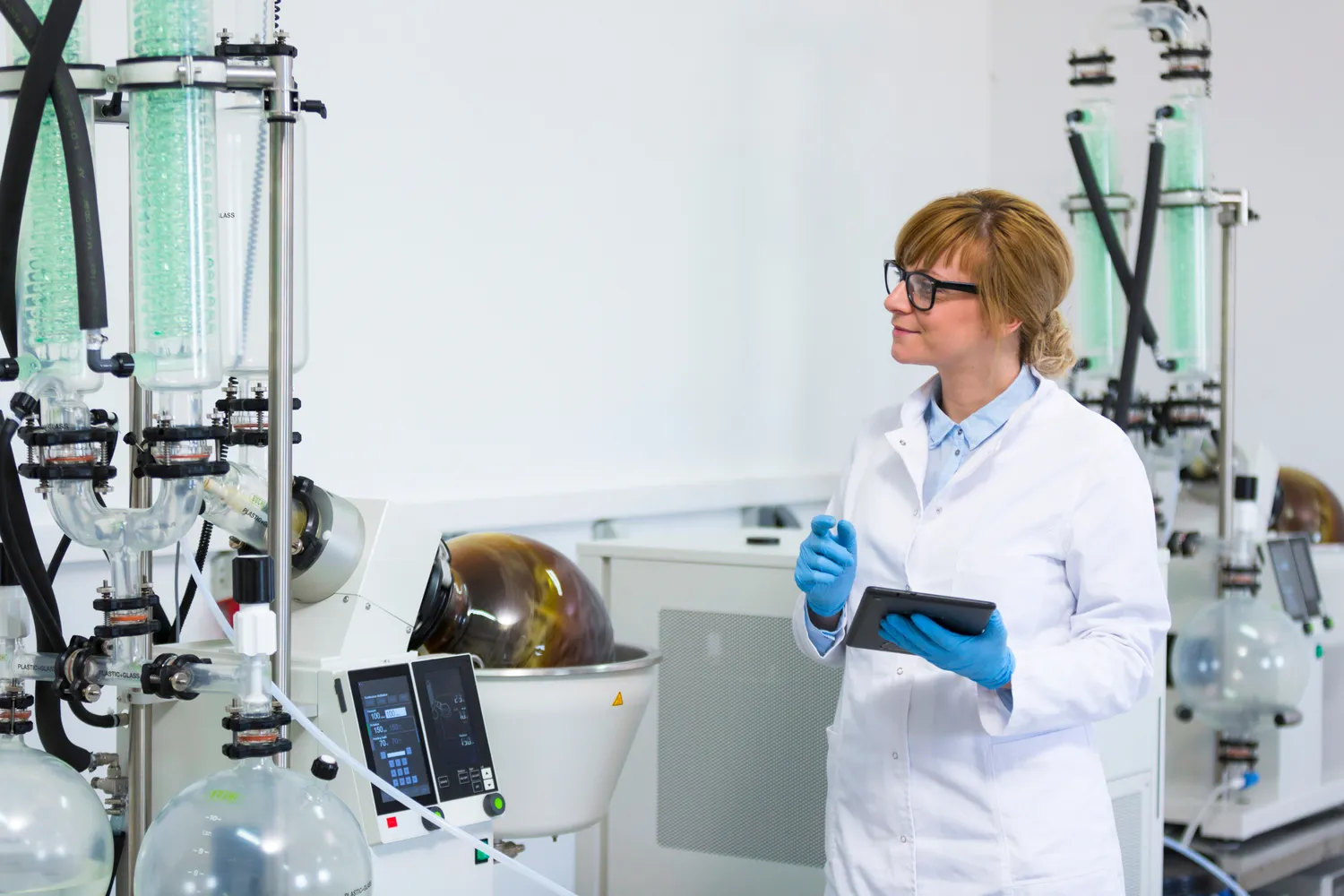
Destylacja prosta i frakcyjna to dwa podstawowe rodzaje procesów destylacyjnych, które różnią się zarówno metodą przeprowadzania, jak i zastosowaniami. Destylacja prosta jest najprostszą formą tego procesu i polega na podgrzewaniu cieczy do jej punktu wrzenia oraz zbieraniu skroplonej pary. Jest to skuteczna metoda dla mieszanin zawierających substancje o znacznie różnych temperaturach wrzenia. Z kolei destylacja frakcyjna jest bardziej skomplikowanym procesem, który wykorzystuje kolumny destylacyjne do wielokrotnego skraplania i parowania składników. Dzięki temu możliwe jest oddzielenie substancji o zbliżonych temperaturach wrzenia. Destylacja frakcyjna jest szczególnie przydatna w przypadku bardziej złożonych mieszanin, takich jak ropa naftowa czy różne rozpuszczalniki organiczne.
Jakie sprzęty są niezbędne do przeprowadzenia destylacji
Aby przeprowadzić proces destylacji rozpuszczalników, niezbędne jest posiadanie odpowiedniego sprzętu laboratoryjnego lub przemysłowego. Podstawowym elementem wyposażenia jest aparat destylacyjny, który może mieć różne formy w zależności od rodzaju destylacji. W przypadku destylacji prostej wystarczy prosty zestaw składający się z kolby grzewczej, chłodnicy oraz naczynia odbierającego skroploną ciecz. Natomiast dla destylacji frakcyjnej konieczne są bardziej zaawansowane urządzenia takie jak kolumny frakcyjne, które umożliwiają wielokrotne skraplanie i parowanie składników. Oprócz tego ważne są także termometry do monitorowania temperatury wrzenia oraz manometry do pomiaru ciśnienia wewnętrznego aparatu. W przypadku pracy z substancjami lotnymi lub toksycznymi istotne jest również zapewnienie odpowiednich systemów wentylacyjnych oraz zabezpieczeń ochronnych dla osób pracujących z tymi materiałami.
Jakie są kluczowe czynniki wpływające na efektywność destylacji
Efektywność procesu destylacji rozpuszczalników jest uzależniona od wielu czynników, które mogą znacząco wpłynąć na jakość i wydajność uzyskanego produktu. Jednym z najważniejszych elementów jest temperatura, która musi być precyzyjnie kontrolowana, aby zapewnić optymalne warunki dla parowania i skraplania. Zbyt wysoka temperatura może prowadzić do niepożądanych reakcji chemicznych, podczas gdy zbyt niska może skutkować niepełnym oddzieleniem składników. Kolejnym istotnym czynnikiem jest ciśnienie, które również wpływa na temperatury wrzenia substancji. W przypadku destylacji pod ciśnieniem można obniżyć temperaturę wrzenia, co pozwala na separację wrażliwych składników bez ich degradacji. Dodatkowo, konstrukcja kolumny destylacyjnej oraz jej wysokość mają kluczowe znaczenie dla efektywności separacji. Wyższe kolumny umożliwiają dłuższy kontakt pary z cieczą, co zwiększa czystość uzyskiwanego produktu.
Jakie są najczęstsze błędy popełniane podczas destylacji
Podczas przeprowadzania procesu destylacji rozpuszczalników istnieje wiele pułapek, w które można wpaść, co może prowadzić do nieefektywnych wyników lub nawet niebezpiecznych sytuacji. Jednym z najczęstszych błędów jest niewłaściwe ustawienie temperatury grzania. Zbyt szybkie podgrzewanie cieczy może prowadzić do gwałtownego wrzenia i powstawania piany, co z kolei może skutkować utratą cennych składników w procesie. Kolejnym problemem jest niewłaściwe dobranie sprzętu, co może ograniczyć efektywność separacji. Na przykład użycie kolby o niewłaściwej pojemności lub chłodnicy o zbyt małej powierzchni chłodzącej może prowadzić do problemów z kondensacją pary. Inne błędy obejmują brak odpowiedniej wentylacji w laboratorium oraz niedostateczne zabezpieczenia osobiste, co zwiększa ryzyko wystąpienia niebezpiecznych sytuacji.
Jakie są różnice między destylacją a innymi metodami separacji
Destylacja rozpuszczalników jest jedną z wielu metod separacji składników mieszanin chemicznych, ale różni się od innych technik zarówno zasadą działania, jak i zastosowaniami. Na przykład ekstrakcja to metoda polegająca na rozdzieleniu składników na podstawie ich rozpuszczalności w różnych rozpuszczalnikach. W przeciwieństwie do destylacji, ekstrakcja często nie wymaga podgrzewania i może być stosowana do substancji termolabilnych, które mogłyby ulec degradacji w wysokiej temperaturze. Inną popularną metodą jest chromatografia, która wykorzystuje różnice w adhezji składników do fazy stacjonarnej i ruchomej. Chromatografia jest niezwykle precyzyjna i pozwala na separację bardzo małych ilości substancji, ale wymaga bardziej skomplikowanego sprzętu i procedur niż destylacja. Z kolei filtracja to technika mechaniczna, która oddziela cząstki stałe od cieczy lub gazu na podstawie ich wielkości.
Jakie są zalety i wady destylacji rozpuszczalników
Destylacja rozpuszczalników ma wiele zalet, które sprawiają, że jest to jedna z najczęściej stosowanych metod separacyjnych w przemyśle i laboratoriach chemicznych. Przede wszystkim pozwala na uzyskanie wysokiej czystości produktów końcowych dzięki selektywnemu oddzielaniu składników na podstawie ich temperatur wrzenia. Jest to szczególnie istotne w produkcji alkoholi oraz w syntezach chemicznych, gdzie czystość reagentów ma kluczowe znaczenie dla wyników reakcji. Ponadto proces ten jest stosunkowo prosty do przeprowadzenia i wymaga minimalnej ilości dodatkowych substancji chemicznych. Jednakże istnieją również pewne wady związane z destylacją. Proces ten może być czasochłonny i wymaga znacznych nakładów energii ze względu na konieczność podgrzewania cieczy do wysokich temperatur.
Jakie są nowoczesne technologie wspierające proces destylacji
W ostatnich latach rozwój technologii przyczynił się do znacznego usprawnienia procesów destylacyjnych poprzez wprowadzenie nowoczesnych rozwiązań inżynieryjnych oraz automatyzację procesów. Jednym z takich innowacyjnych podejść jest zastosowanie technologii membranowej, która pozwala na separację składników bez konieczności podgrzewania cieczy. Membrany selektywnie przepuszczają określone składniki, co znacznie zmniejsza zużycie energii oraz ryzyko degradacji termicznej substancji. Kolejnym przykładem są systemy automatyzacji procesów przemysłowych, które umożliwiają precyzyjne monitorowanie i kontrolowanie parametrów pracy aparatury destylacyjnej w czasie rzeczywistym. Dzięki temu możliwe jest optymalizowanie warunków pracy oraz minimalizowanie ryzyka błędów ludzkich.
Jakie są przyszłe kierunki badań nad destylacją rozpuszczalników
Przyszłość badań nad destylacją rozpuszczalników wydaje się obiecująca dzięki ciągłemu postępowi technologicznemu oraz rosnącemu zainteresowaniu ekologicznymi metodami produkcji chemicznej. Jednym z głównych kierunków badań jest rozwój bardziej efektywnych systemów odzysku energii podczas procesu destylacyjnego. Badacze poszukują nowych materiałów izolacyjnych oraz technologii recyklingu ciepła, które mogłyby znacznie obniżyć koszty energetyczne związane z tym procesem. Innym interesującym obszarem badań są biotechnologie związane z wykorzystaniem mikroorganizmów do produkcji rozpuszczalników organicznych oraz ich późniejszej separacji za pomocą innowacyjnych metod destylacyjnych. W kontekście ochrony środowiska coraz większą uwagę zwraca się również na rozwój metod minimalizujących emisję szkodliwych substancji podczas procesu destylacji oraz promujących użycie odnawialnych źródeł surowców chemicznych.
Jakie są różnice w destylacji rozpuszczalników w różnych branżach
Destylacja rozpuszczalników jest stosowana w wielu branżach, a jej zastosowanie różni się w zależności od specyfiki danej dziedziny. W przemyśle farmaceutycznym proces ten jest kluczowy dla uzyskiwania czystych substancji czynnych, które muszą spełniać rygorystyczne normy jakości. Z kolei w przemyśle spożywczym destylacja jest wykorzystywana do produkcji alkoholi oraz aromatów, gdzie czystość i smak są niezwykle ważne. W sektorze petrochemicznym destylacja służy do separacji różnych frakcji ropy naftowej, co jest kluczowe dla produkcji paliw oraz innych chemikaliów. Każda z tych branż ma swoje unikalne wymagania dotyczące efektywności, czystości i bezpieczeństwa procesu destylacji, co sprawia, że techniki oraz sprzęt używany w tych dziedzinach mogą się znacznie różnić.