Budowa maszyn pneumatycznych
Budowa maszyn pneumatycznych opiera się na kilku kluczowych elementach, które są niezbędne do ich prawidłowego funkcjonowania. Pierwszym z nich jest sprężarka, która odpowiada za wytwarzanie sprężonego powietrza. Sprężarki mogą być różnego typu, w tym tłokowe, śrubowe czy wirnikowe, a ich wybór zależy od specyficznych potrzeb aplikacji. Kolejnym istotnym elementem są zbiorniki na sprężone powietrze, które pozwalają na gromadzenie energii w postaci sprężonego powietrza i jej późniejsze wykorzystanie. Ważnym komponentem są również zawory, które kontrolują przepływ powietrza w systemie. Zawory te mogą być ręczne lub automatyczne i mają kluczowe znaczenie dla precyzyjnego sterowania pracą maszyny. Oprócz tego, nie można zapomnieć o siłownikach pneumatycznych, które przekształcają energię sprężonego powietrza na ruch mechaniczny. Siłowniki te mogą być cylindryczne lub membranowe i są wykorzystywane w wielu różnych aplikacjach przemysłowych. Wreszcie, do budowy maszyn pneumatycznych niezbędne są także różnego rodzaju przewody i złącza, które zapewniają odpowiednią komunikację między poszczególnymi komponentami systemu.
Jakie są zastosowania maszyn pneumatycznych w przemyśle
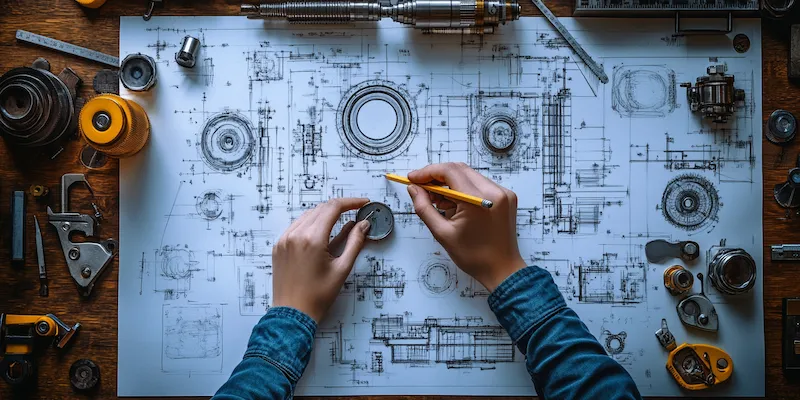
Maszyny pneumatyczne znajdują szerokie zastosowanie w różnych gałęziach przemysłu dzięki swojej wszechstronności oraz efektywności. W przemyśle produkcyjnym są często wykorzystywane do automatyzacji procesów montażowych, gdzie siłowniki pneumatyczne umożliwiają szybkie i precyzyjne ruchy robocze. Dzięki temu możliwe jest zwiększenie wydajności produkcji oraz redukcja kosztów pracy. W branży motoryzacyjnej maszyny pneumatyczne służą do malowania samochodów, gdzie sprężone powietrze jest używane do rozpylania farby w sposób równomierny i kontrolowany. W sektorze spożywczym maszyny te są wykorzystywane do pakowania produktów, co pozwala na zachowanie wysokich standardów higieny oraz efektywności operacyjnej. W logistyce i magazynowaniu maszyny pneumatyczne wspierają procesy transportowe oraz sortujące, co przyspiesza obsługę towarów. Dodatkowo w branży budowlanej stosuje się narzędzia pneumatyczne do wiercenia czy cięcia materiałów budowlanych, co znacznie ułatwia pracę i zwiększa jej bezpieczeństwo.
Jakie są zalety i wady maszyn pneumatycznych
Maszyny pneumatyczne mają wiele zalet, które przyciągają uwagę inżynierów oraz menedżerów produkcji. Przede wszystkim charakteryzują się dużą niezawodnością i prostotą obsługi, co sprawia, że są łatwe do wdrożenia w różnych środowiskach przemysłowych. Ponadto ich konstrukcja jest zazwyczaj lżejsza niż maszyn elektrycznych czy hydraulicznych, co ułatwia ich transport oraz instalację. Maszyny te są również odporne na działanie wysokich temperatur oraz substancji chemicznych, co czyni je idealnym rozwiązaniem w trudnych warunkach pracy. Jednakże istnieją także pewne wady związane z ich użytkowaniem. Jedną z nich jest konieczność regularnej konserwacji systemu sprężonego powietrza oraz monitorowania jego ciśnienia, co może wiązać się z dodatkowymi kosztami eksploatacyjnymi. Innym problemem może być hałas generowany przez sprężarki oraz inne elementy systemu, co wymaga zastosowania odpowiednich rozwiązań akustycznych w miejscach pracy.
Jakie innowacje wpływają na rozwój maszyn pneumatycznych
W ostatnich latach rozwój technologii wpłynął na ewolucję maszyn pneumatycznych, prowadząc do pojawienia się innowacyjnych rozwiązań zwiększających ich wydajność oraz funkcjonalność. Jednym z najważniejszych trendów jest integracja systemów pneumatycznych z nowoczesnymi technologiami cyfrowymi i automatyzacją przemysłową. Dzięki zastosowaniu czujników oraz systemów monitorujących możliwe jest zbieranie danych na temat pracy maszyn w czasie rzeczywistym, co pozwala na optymalizację procesów produkcyjnych oraz szybsze reagowanie na ewentualne awarie. Kolejnym istotnym kierunkiem rozwoju jest miniaturyzacja komponentów pneumatycznych, co pozwala na tworzenie bardziej kompaktowych i elastycznych rozwiązań dostosowanych do specyficznych potrzeb klientów. Innowacyjne materiały stosowane w budowie siłowników czy zaworów zwiększają ich trwałość oraz odporność na uszkodzenia mechaniczne czy chemiczne. Również rozwój technologii sprężarek prowadzi do poprawy efektywności energetycznej tych urządzeń, co ma kluczowe znaczenie dla obniżenia kosztów eksploatacyjnych całego systemu.
Jakie są najczęstsze problemy z maszynami pneumatycznymi
Maszyny pneumatyczne, mimo swojej niezawodności, mogą napotykać różne problemy, które wpływają na ich wydajność i funkcjonalność. Jednym z najczęstszych problemów jest wyciek sprężonego powietrza, który może prowadzić do znacznych strat energetycznych oraz obniżenia efektywności pracy maszyny. Wyciek ten często występuje w miejscach połączeń przewodów, zaworów czy siłowników, dlatego regularne inspekcje i konserwacja systemu są kluczowe dla utrzymania jego sprawności. Innym powszechnym problemem jest zanieczyszczenie sprężonego powietrza, które może prowadzić do uszkodzenia komponentów maszyny oraz obniżenia jakości produkcji. Zanieczyszczenia mogą pochodzić z różnych źródeł, takich jak wilgoć, olej czy cząstki stałe, dlatego stosowanie filtrów oraz separatorów wody jest niezbędne w każdym systemie pneumatycznym. Kolejnym wyzwaniem jest niewłaściwe ciśnienie robocze, które może prowadzić do nieprawidłowego działania siłowników oraz zaworów. Zbyt niskie ciśnienie może skutkować słabą wydajnością, podczas gdy zbyt wysokie ciśnienie może prowadzić do uszkodzeń komponentów. Oprócz tego, awarie sprężarek mogą być kolejnym istotnym problemem, który wpływa na cały system pneumatyczny.
Jakie są przyszłościowe kierunki rozwoju maszyn pneumatycznych
Przyszłość maszyn pneumatycznych zapowiada się obiecująco dzięki ciągłemu rozwojowi technologii oraz rosnącemu zapotrzebowaniu na efektywne rozwiązania w przemyśle. Jednym z kluczowych kierunków rozwoju jest automatyzacja procesów produkcyjnych, która pozwala na zwiększenie wydajności oraz redukcję kosztów operacyjnych. Wprowadzenie robotyzacji do systemów pneumatycznych umożliwia precyzyjne sterowanie ruchami maszyn oraz ich synchronizację z innymi urządzeniami w linii produkcyjnej. Również rozwój sztucznej inteligencji i uczenia maszynowego ma potencjał do znaczącego poprawienia efektywności systemów pneumatycznych poprzez optymalizację procesów oraz predykcję awarii. Kolejnym ważnym aspektem jest zastosowanie technologii Internetu Rzeczy (IoT), która umożliwia zbieranie danych z maszyn w czasie rzeczywistym i ich analizę w celu podejmowania lepszych decyzji operacyjnych. Dodatkowo rosnąca świadomość ekologiczna społeczeństwa skłania producentów do poszukiwania bardziej zrównoważonych rozwiązań w budowie maszyn pneumatycznych, takich jak wykorzystanie materiałów odnawialnych czy projektowanie systemów o niższym zużyciu energii.
Jakie są koszty eksploatacji maszyn pneumatycznych
Koszty eksploatacji maszyn pneumatycznych mogą być zróżnicowane i zależą od wielu czynników, takich jak rodzaj zastosowanej technologii, intensywność użytkowania oraz warunki pracy. Kluczowym elementem wpływającym na te koszty jest zużycie energii związane z działaniem sprężarek powietrza. Sprężarki stanowią główny element systemu pneumatycznego i ich efektywność energetyczna ma bezpośredni wpływ na całkowite koszty operacyjne. Warto inwestować w nowoczesne sprężarki o wysokiej wydajności energetycznej, które mogą znacznie obniżyć rachunki za energię elektryczną. Kolejnym istotnym czynnikiem są koszty konserwacji i serwisowania maszyn. Regularne przeglądy techniczne oraz wymiana zużytych części są niezbędne dla zapewnienia długotrwałego i niezawodnego działania systemu pneumatycznego. Dodatkowo warto uwzględnić koszty związane z zakupem materiałów eksploatacyjnych, takich jak filtry czy oleje do sprężarek. Koszty te mogą się różnić w zależności od producenta i jakości używanych komponentów. Należy również pamiętać o potencjalnych kosztach związanych z przestojami spowodowanymi awariami maszyn, które mogą prowadzić do strat finansowych dla przedsiębiorstwa.
Jakie są różnice między maszynami pneumatycznymi a hydraulicznymi
Maszyny pneumatyczne i hydrauliczne to dwa różne typy technologii stosowanych w automatyce przemysłowej, które mają swoje unikalne cechy oraz zastosowania. Główna różnica między nimi polega na medium roboczym: maszyny pneumatyczne wykorzystują sprężone powietrze jako źródło energii, podczas gdy maszyny hydrauliczne opierają się na cieczy hydraulicznej. Dzięki temu maszyny pneumatyczne charakteryzują się lżejszą konstrukcją oraz prostszymi systemami sterującymi, co sprawia, że są łatwiejsze w obsłudze i konserwacji. Z drugiej strony maszyny hydrauliczne oferują większą siłę roboczą przy mniejszych rozmiarach siłowników, co czyni je idealnymi do zastosowań wymagających dużych momentów obrotowych lub dużych sił tłoczenia. Kolejną istotną różnicą jest szybkość działania: maszyny pneumatyczne zazwyczaj działają szybciej niż hydrauliczne ze względu na mniejsze opory wewnętrzne związane z przepływem powietrza w porównaniu do cieczy hydraulicznych. Jednakże maszyny hydrauliczne mają przewagę w zakresie precyzyjnego sterowania ruchem oraz możliwości pracy przy dużych obciążeniach przez dłuższy czas bez ryzyka przegrzewania się układów roboczych.
Jakie są najważniejsze normy dotyczące budowy maszyn pneumatycznych
Budowa maszyn pneumatycznych podlega różnym normom i regulacjom mającym na celu zapewnienie bezpieczeństwa użytkowników oraz efektywności działania tych urządzeń. Jedną z kluczowych norm jest norma ISO 4414 dotycząca systemów pneumatycznych i ich elementów składowych. Norma ta określa zasady projektowania, instalacji oraz eksploatacji systemów pneumatycznych w sposób zapewniający bezpieczeństwo i niezawodność ich działania. Inną istotną normą jest norma EN 983 dotycząca bezpieczeństwa urządzeń wykonujących pracę za pomocą sprężonego powietrza, która wskazuje wymagania dotyczące konstrukcji i użytkowania tych urządzeń w kontekście ochrony zdrowia i życia pracowników. Ważne są także normy dotyczące jakości sprężonego powietrza, takie jak ISO 8573-1, która definiuje klasy czystości powietrza wykorzystywanego w systemach pneumatycznych oraz metody jego pomiaru. Przestrzeganie tych norm jest kluczowe dla zapewnienia wysokiej jakości produktów oraz bezpieczeństwa pracy w zakładach przemysłowych korzystających z technologii pneumatycznej.