Projektowanie i budowa maszy
Projektowanie i budowa maszyn to proces, który wymaga staranności oraz przemyślanej koncepcji na każdym etapie. Kluczowym pierwszym krokiem jest analiza potrzeb i wymagań klienta, co pozwala na zrozumienie, jakie funkcje ma spełniać projektowana maszyna. Następnie przechodzi się do fazy wstępnego projektowania, gdzie tworzone są pierwsze szkice oraz modele koncepcyjne. W tym etapie inżynierowie często korzystają z narzędzi CAD, które umożliwiają wizualizację pomysłów oraz wprowadzenie ewentualnych poprawek jeszcze przed rozpoczęciem produkcji. Kolejnym krokiem jest szczegółowe projektowanie, które obejmuje dobór odpowiednich materiałów oraz komponentów, a także obliczenia wytrzymałościowe i analizy dynamiki maszyny. Po zakończeniu fazy projektowej następuje etap prototypowania, gdzie tworzony jest pierwszy model maszyny, który poddawany jest testom. Testy te są niezbędne do wykrycia ewentualnych błędów oraz usterek, które mogą wystąpić podczas normalnej eksploatacji.
Jakie technologie są wykorzystywane w budowie maszyn?
W dzisiejszych czasach projektowanie i budowa maszyn opierają się na zaawansowanych technologiach, które znacznie zwiększają efektywność oraz precyzję całego procesu. Jednym z najważniejszych narzędzi wykorzystywanych w tym zakresie są systemy komputerowego wspomagania projektowania (CAD), które umożliwiają inżynierom tworzenie skomplikowanych modeli 3D oraz symulacji działania maszyny. Dzięki temu można szybko wprowadzać zmiany i optymalizować konstrukcję przed rozpoczęciem produkcji. Kolejną istotną technologią jest druk 3D, który pozwala na szybkie prototypowanie elementów maszyn oraz testowanie ich właściwości fizycznych bez konieczności angażowania dużych zasobów materiałowych. W procesie budowy maszyn coraz częściej wykorzystuje się również automatyzację i robotyzację, co znacząco przyspiesza produkcję oraz minimalizuje ryzyko błędów ludzkich. Dodatkowo zastosowanie technologii IoT (Internet of Things) w maszynach przemysłowych umożliwia zbieranie danych w czasie rzeczywistym oraz monitorowanie stanu technicznego urządzeń, co przekłada się na lepsze zarządzanie procesami produkcyjnymi i utrzymanie ruchu.
Jakie są najczęstsze problemy podczas budowy maszyn?
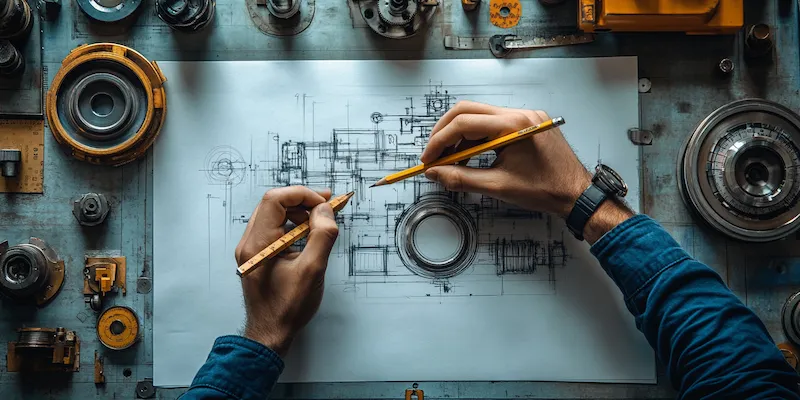
Podczas projektowania i budowy maszyn mogą wystąpić różnorodne problemy, które mogą wpłynąć na jakość końcowego produktu oraz czas realizacji projektu. Jednym z najczęstszych wyzwań jest niewłaściwe określenie wymagań klienta na początku procesu, co może prowadzić do nieporozumień i konieczności wprowadzania kosztownych zmian w późniejszych etapach. Innym problemem mogą być ograniczenia technologiczne związane z dostępnością materiałów lub komponentów, które mogą opóźnić produkcję lub wpłynąć na jakość finalnego produktu. Również błędy w obliczeniach wytrzymałościowych czy dynamice maszyny mogą prowadzić do poważnych usterek podczas testów prototypu. Często zdarza się także, że zespół projektowy nie ma wystarczającej komunikacji między sobą, co może skutkować brakiem spójności w projekcie i koniecznością jego rewizji. Dodatkowo zmieniające się przepisy prawne dotyczące bezpieczeństwa maszyn mogą wymusić dodatkowe modyfikacje już zaprojektowanych urządzeń.
Jakie są przyszłościowe kierunki rozwoju w branży maszynowej?
Przemysł maszynowy stoi obecnie przed wieloma wyzwaniami i możliwościami rozwoju, które mogą znacząco wpłynąć na przyszłość tej branży. Wśród najważniejszych trendów można zauważyć rosnącą automatyzację procesów produkcyjnych oraz integrację sztucznej inteligencji w systemach sterujących maszynami. Dzięki temu możliwe będzie osiągnięcie większej efektywności operacyjnej oraz redukcja kosztów produkcji poprzez optymalizację procesów w czasie rzeczywistym. Kolejnym kierunkiem rozwoju jest zastosowanie technologii zrównoważonego rozwoju, która kładzie nacisk na minimalizację wpływu produkcji na środowisko naturalne poprzez stosowanie materiałów odnawialnych oraz energooszczędnych rozwiązań technologicznych. Warto również zwrócić uwagę na rozwój Internetu Rzeczy (IoT), który umożliwia gromadzenie danych z różnych urządzeń i ich analizę w celu poprawy efektywności działania maszyn oraz przewidywania awarii zanim one nastąpią.
Jakie umiejętności są kluczowe dla inżynierów maszynowych?
W dziedzinie projektowania i budowy maszyn, inżynierowie muszą posiadać szereg umiejętności, które pozwolą im skutecznie realizować złożone projekty. Kluczową kompetencją jest znajomość zasad mechaniki oraz materiałoznawstwa, co umożliwia dobór odpowiednich komponentów oraz ocenę ich właściwości w kontekście planowanej eksploatacji. Umiejętność posługiwania się nowoczesnymi narzędziami CAD jest niezbędna, aby móc tworzyć precyzyjne modele 3D oraz przeprowadzać symulacje działania maszyn. Również zdolności analityczne są niezwykle ważne, ponieważ inżynierowie muszą być w stanie ocenić wyniki testów prototypów oraz wprowadzać niezbędne poprawki do projektu. Komunikacja interpersonalna odgrywa istotną rolę w pracy zespołowej, dlatego inżynierowie powinni umieć efektywnie współpracować z innymi członkami zespołu oraz z klientami. Wreszcie, umiejętność zarządzania projektami staje się coraz bardziej pożądana, ponieważ pozwala na efektywne planowanie działań oraz kontrolowanie budżetu i terminów realizacji.
Jakie są najważniejsze normy i standardy w budowie maszyn?
Projektowanie i budowa maszyn wiążą się z przestrzeganiem licznych norm i standardów, które mają na celu zapewnienie bezpieczeństwa użytkowników oraz niezawodności urządzeń. W Europie kluczowym dokumentem regulującym te kwestie jest dyrektywa maszynowa 2006/42/WE, która określa wymagania dotyczące bezpieczeństwa maszyn i urządzeń. Zgodność z tą dyrektywą jest niezbędna do uzyskania oznakowania CE, co pozwala na legalne wprowadzenie maszyny na rynek europejski. Oprócz tego istnieją różne normy ISO, takie jak ISO 9001 dotycząca systemu zarządzania jakością czy ISO 12100 dotycząca bezpieczeństwa maszyn. Normy te pomagają firmom w organizacji procesów produkcyjnych oraz w zapewnieniu wysokiej jakości produktów. Warto również zwrócić uwagę na normy dotyczące ochrony środowiska, takie jak ISO 14001, które promują zrównoważony rozwój i minimalizację wpływu produkcji na otoczenie.
Jakie są wyzwania związane z automatyzacją procesów w branży maszynowej?
Automatyzacja procesów w branży maszynowej przynosi wiele korzyści, jednak wiąże się również z szeregiem wyzwań, które należy uwzględnić podczas projektowania i budowy maszyn. Jednym z głównych problemów jest konieczność dostosowania istniejących systemów produkcyjnych do nowych technologii automatyzacyjnych. Wiele zakładów przemysłowych dysponuje starzejącymi się urządzeniami, które mogą być trudne do integracji z nowoczesnymi rozwiązaniami. Dodatkowo automatyzacja wymaga znacznych inwestycji finansowych, co może stanowić barierę dla mniejszych przedsiębiorstw. Kolejnym wyzwaniem jest potrzeba przeszkolenia pracowników w zakresie obsługi nowych technologii oraz systemów informatycznych, co wiąże się z dodatkowymi kosztami i czasem potrzebnym na adaptację. Również kwestie związane z bezpieczeństwem pracy stają się bardziej skomplikowane w kontekście automatyzacji – konieczne jest zapewnienie odpowiednich zabezpieczeń oraz procedur awaryjnych w przypadku awarii systemu automatycznego.
Jakie są korzyści płynące z zastosowania technologii IoT w maszynach?
Wprowadzenie technologii Internetu Rzeczy (IoT) do projektowania i budowy maszyn otwiera nowe możliwości dla przemysłu. Dzięki IoT maszyny mogą gromadzić dane o swoim działaniu w czasie rzeczywistym, co pozwala na bieżąco monitorować ich wydajność oraz stan techniczny. Tego rodzaju informacje mogą być wykorzystywane do przewidywania awarii jeszcze przed ich wystąpieniem, co znacząco zwiększa efektywność utrzymania ruchu oraz minimalizuje przestoje produkcyjne. Kolejną korzyścią jest możliwość optymalizacji procesów produkcyjnych poprzez analizę danych zbieranych przez maszyny – przedsiębiorstwa mogą dostosowywać parametry pracy do zmieniających się warunków lub potrzeb klientów. IoT umożliwia również zdalne zarządzanie maszynami oraz ich diagnostykę, co pozwala na szybsze reagowanie na problemy oraz ogranicza koszty związane z serwisowaniem sprzętu.
Jakie są perspektywy rozwoju robotyzacji w branży maszynowej?
Robotyzacja staje się jednym z kluczowych trendów w branży maszynowej, a jej rozwój niesie ze sobą wiele korzyści zarówno dla producentów maszyn, jak i dla samych użytkowników tych urządzeń. Zastosowanie robotów przemysłowych pozwala na zwiększenie wydajności produkcji poprzez automatyzację rutynowych czynności oraz eliminację błędów ludzkich. Roboty są w stanie pracować przez długie godziny bez przerwy, co przekłada się na skrócenie czasu realizacji zamówień i zwiększenie elastyczności produkcji. W miarę postępu technologicznego roboty stają się coraz bardziej zaawansowane – potrafią uczyć się nowych umiejętności dzięki algorytmom uczenia maszynowego oraz współpracować ze sobą w ramach zespołów roboczych. To otwiera nowe możliwości zastosowania robotyzacji w różnych sektorach przemysłu, od montażu po pakowanie czy kontrolę jakości. Jednak rozwój robotyzacji wiąże się również z wyzwaniami – konieczne jest dostosowanie infrastruktury zakładów produkcyjnych do nowych technologii oraz przeszkolenie pracowników w zakresie obsługi robotów.
Jakie są trendy związane z ekologicznymi rozwiązaniami w projektowaniu maszyn?
W obliczu rosnącej świadomości ekologicznej społeczeństwa oraz zaostrzających się regulacji dotyczących ochrony środowiska, projektowanie i budowa maszyn coraz częściej uwzględniają aspekty ekologiczne. Trend ten obejmuje zarówno wybór materiałów przyjaznych dla środowiska, jak i optymalizację procesów produkcyjnych pod kątem minimalizacji zużycia energii oraz odpadów. Producenci starają się stosować materiały odnawialne lub recyklingowane tam, gdzie to możliwe, co przyczynia się do zmniejszenia śladu ekologicznego powstających urządzeń. Ponadto wiele firm inwestuje w technologie energooszczędne oraz systemy odzysku ciepła czy energii elektrycznej podczas eksploatacji maszyn. Ekologiczne podejście do projektowania obejmuje także myślenie o cyklu życia produktu – projektanci starają się tworzyć maszyny łatwe do demontażu i recyklingu po zakończeniu ich użytkowania.