Destylator przemysłowy
Destylator przemysłowy to urządzenie służące do oddzielania składników cieczy na podstawie różnicy ich temperatur wrzenia. Proces destylacji jest kluczowy w wielu branżach, takich jak chemiczna, petrochemiczna czy spożywcza. W destylatorze przemysłowym ciecz jest podgrzewana, co powoduje jej parowanie. Powstała para następnie przechodzi przez skraplacz, gdzie ulega kondensacji i wraca do stanu ciekłego. Dzięki temu możliwe jest uzyskanie czystszych frakcji substancji oraz ich efektywne rozdzielenie. Destylatory przemysłowe mogą mieć różne konstrukcje, w tym kolumnowe i prostokątne, a ich wybór zależy od specyfiki procesu technologicznego. W przemyśle chemicznym destylatory są wykorzystywane do produkcji rozpuszczalników, alkoholi oraz innych substancji chemicznych. W branży spożywczej natomiast destylacja jest kluczowa w produkcji napojów alkoholowych, takich jak whisky czy wódka.
Jakie są rodzaje destylatorów przemysłowych i ich zastosowania
W przemyśle istnieje wiele rodzajów destylatorów, które różnią się konstrukcją oraz zastosowaniem. Najpopularniejsze z nich to destylatory kolumnowe oraz prostokątne. Destylatory kolumnowe charakteryzują się dużą efektywnością separacji dzięki zastosowaniu kolumny z wypełnieniem lub talerzami, które zwiększają powierzchnię kontaktu między parą a cieczą. Tego rodzaju urządzenia są powszechnie stosowane w rafineriach ropy naftowej do produkcji paliw oraz w przemyśle chemicznym do uzyskiwania czystych substancji chemicznych. Z kolei destylatory prostokątne są bardziej kompaktowe i często wykorzystywane w mniejszych zakładach produkcyjnych, gdzie nie ma potrzeby stosowania zaawansowanych technologii separacji. W przypadku produkcji alkoholi, destylatory mogą być wyposażone w dodatkowe elementy, takie jak chłodnice czy zbiorniki fermentacyjne. Innym rodzajem są destylatory próżniowe, które umożliwiają prowadzenie procesów w obniżonym ciśnieniu, co pozwala na destylację substancji o wysokiej temperaturze wrzenia bez ryzyka ich rozkładu.
Jakie są korzyści z używania destylatora przemysłowego
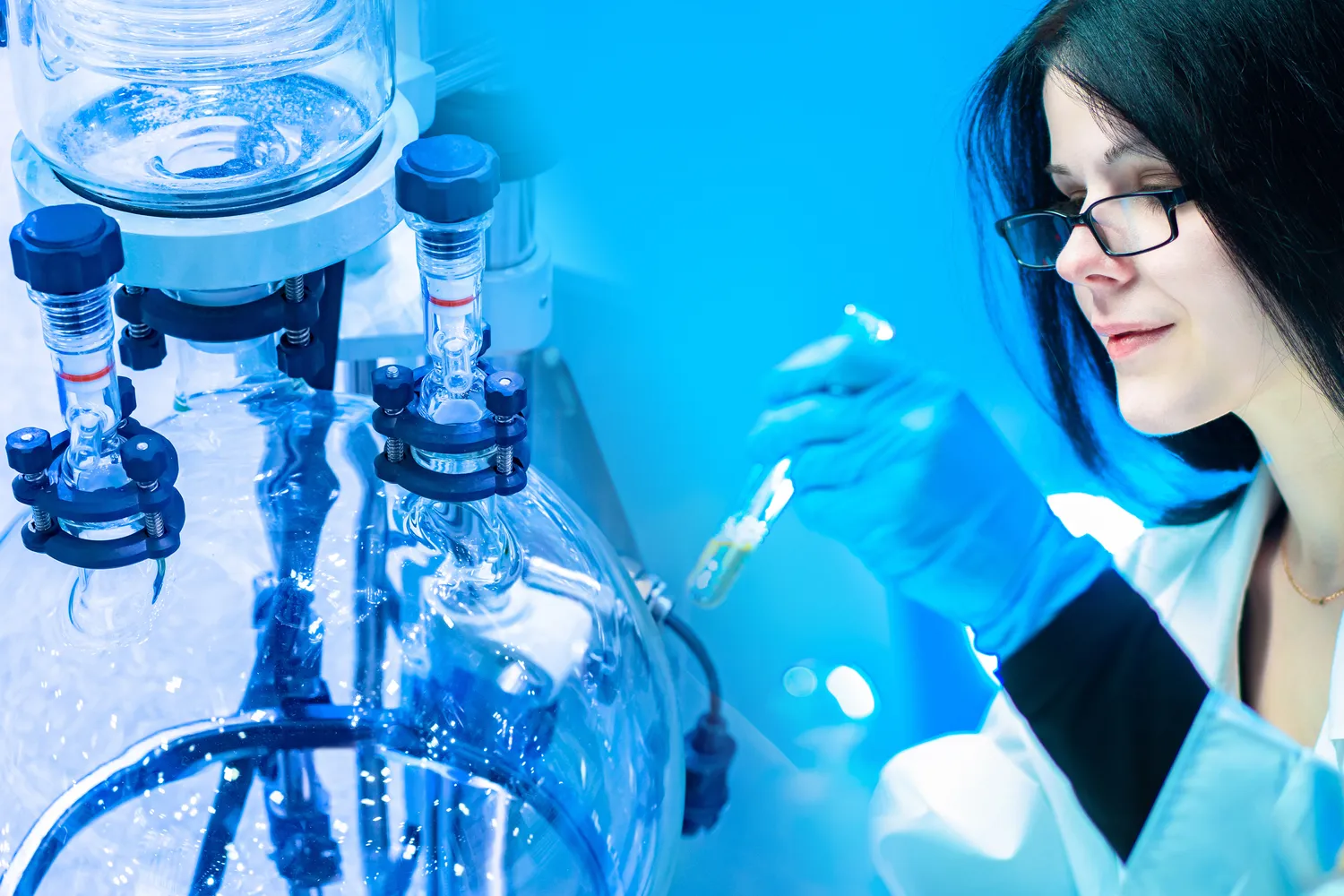
Używanie destylatora przemysłowego niesie ze sobą wiele korzyści zarówno dla producentów, jak i dla końcowych użytkowników produktów. Przede wszystkim proces destylacji pozwala na uzyskanie wysokiej czystości substancji chemicznych oraz ich skuteczne rozdzielenie na poszczególne frakcje. Dzięki temu możliwe jest produkowanie wyrobów o ściśle określonych parametrach jakościowych, co jest szczególnie istotne w branżach regulowanych przez normy prawne i standardy jakości. Kolejną zaletą jest możliwość recyklingu surowców – wiele firm wykorzystuje destylatory do odzyskiwania rozpuszczalników czy innych substancji chemicznych z odpadów produkcyjnych, co przyczynia się do zmniejszenia kosztów operacyjnych oraz wpływu na środowisko. Ponadto nowoczesne destylatory są często wyposażone w zaawansowane systemy automatyzacji i monitoringu, co zwiększa wydajność procesów oraz minimalizuje ryzyko błędów ludzkich.
Jakie są wyzwania związane z eksploatacją destylatorów przemysłowych
Mimo licznych korzyści wynikających z użycia destylatorów przemysłowych istnieją także pewne wyzwania związane z ich eksploatacją. Jednym z głównych problemów jest konieczność regularnego serwisowania i konserwacji urządzeń, aby zapewnić ich prawidłowe działanie oraz uniknąć awarii. Niewłaściwie utrzymany destylator może prowadzić do obniżenia jakości produktów końcowych oraz zwiększenia kosztów operacyjnych związanych z naprawami. Kolejnym wyzwaniem jest zarządzanie zużyciem energii – procesy destylacyjne mogą być energochłonne, dlatego ważne jest optymalizowanie parametrów pracy urządzeń oraz wdrażanie nowoczesnych technologii mających na celu zwiększenie efektywności energetycznej. Dodatkowo operatorzy muszą być odpowiednio przeszkoleni w zakresie obsługi i monitorowania pracy destylatorów, aby minimalizować ryzyko błędów czy nieprawidłowości w procesach technologicznych.
Jakie są najnowsze technologie w dziedzinie destylacji przemysłowej
W ostatnich latach technologia destylacji przemysłowej uległa znacznym zmianom, co przyczyniło się do zwiększenia efektywności i wydajności procesów produkcyjnych. Nowoczesne destylatory są często wyposażone w zaawansowane systemy automatyzacji, które umożliwiają zdalne monitorowanie i kontrolę parametrów pracy. Dzięki zastosowaniu czujników i systemów informatycznych operatorzy mogą na bieżąco śledzić temperatury, ciśnienia oraz inne kluczowe wskaźniki, co pozwala na szybką reakcję w przypadku wystąpienia nieprawidłowości. Ponadto rozwój technologii materiałowych umożliwił produkcję komponentów destylatorów odpornych na korozję oraz wysokie temperatury, co zwiększa ich trwałość i niezawodność. Warto również zwrócić uwagę na innowacje w zakresie efektywności energetycznej, takie jak systemy odzysku ciepła, które pozwalają na wykorzystanie energii z procesów destylacyjnych do podgrzewania innych mediów. Dzięki tym rozwiązaniom przedsiębiorstwa mogą znacząco obniżyć koszty operacyjne oraz zmniejszyć swój wpływ na środowisko.
Jakie są kluczowe czynniki wpływające na wybór destylatora przemysłowego
Wybór odpowiedniego destylatora przemysłowego jest kluczowy dla efektywności procesu produkcyjnego i zależy od wielu czynników. Przede wszystkim należy uwzględnić rodzaj substancji, które mają być poddane destylacji. Różne składniki chemiczne mają różne temperatury wrzenia oraz właściwości fizykochemiczne, co wpływa na wybór konstrukcji destylatora. Kolejnym istotnym czynnikiem jest skala produkcji – dla małych zakładów wystarczające mogą być prostsze i tańsze urządzenia, podczas gdy duże zakłady przemysłowe potrzebują bardziej zaawansowanych rozwiązań o wysokiej wydajności. Ważne jest także uwzględnienie kosztów eksploatacji, w tym zużycia energii oraz kosztów serwisowania urządzeń. Przedsiębiorstwa powinny również brać pod uwagę dostępność części zamiennych oraz wsparcia technicznego ze strony producenta. Dodatkowo nie można zapominać o regulacjach prawnych dotyczących bezpieczeństwa pracy oraz ochrony środowiska – wybierając destylator, warto upewnić się, że spełnia on wszystkie obowiązujące normy i standardy.
Jakie są najczęstsze błędy przy obsłudze destylatorów przemysłowych
Obsługa destylatorów przemysłowych wymaga odpowiedniej wiedzy i doświadczenia, a popełnione błędy mogą prowadzić do poważnych konsekwencji zarówno dla jakości produktów, jak i bezpieczeństwa pracy. Jednym z najczęstszych błędów jest niewłaściwe ustawienie parametrów pracy urządzenia, takich jak temperatura czy ciśnienie. Niezgodność tych wartości z wymaganiami procesu może skutkować obniżoną jakością destylatu lub nawet uszkodzeniem sprzętu. Kolejnym problemem jest brak regularnej konserwacji i przeglądów technicznych – zaniedbania w tym zakresie mogą prowadzić do awarii oraz zwiększenia kosztów napraw. Operatorzy często popełniają także błędy związane z interpretacją danych z systemu monitorowania; niewłaściwe odczyty mogą prowadzić do nieuzasadnionych interwencji lub ignorowania rzeczywistych problemów. Dodatkowo ważne jest przestrzeganie procedur bezpieczeństwa – nieprzestrzeganie zasad BHP może prowadzić do poważnych wypadków w miejscu pracy.
Jakie są przyszłe kierunki rozwoju technologii destylacji przemysłowej
Przemysłowa technologia destylacji stoi przed wieloma wyzwaniami i możliwościami rozwoju w nadchodzących latach. Jednym z głównych kierunków jest dalsza automatyzacja procesów produkcyjnych, co pozwoli na zwiększenie wydajności oraz redukcję błędów ludzkich. Systemy sztucznej inteligencji mogą być wykorzystywane do analizy danych operacyjnych i optymalizacji parametrów pracy destylatorów w czasie rzeczywistym. Również rozwój technologii cyfrowych umożliwia lepsze zarządzanie danymi oraz integrację różnych procesów produkcyjnych w ramach jednego systemu zarządzania. Innym istotnym trendem jest rosnące zainteresowanie zrównoważonym rozwojem i ekologicznymi rozwiązaniami – przedsiębiorstwa będą poszukiwać sposobów na minimalizację zużycia energii oraz emisji substancji szkodliwych podczas procesów destylacyjnych. Technologie odzysku ciepła oraz zastosowanie odnawialnych źródeł energii staną się coraz bardziej popularne w branży. Dodatkowo rozwój nowych materiałów o lepszych właściwościach termicznych i chemicznych może przyczynić się do poprawy efektywności procesów separacyjnych.
Jakie są zastosowania destylatorów przemysłowych w różnych branżach
Destylatory przemysłowe znajdują szerokie zastosowanie w różnych branżach gospodarki, co świadczy o ich wszechstronności i znaczeniu dla współczesnego przemysłu. W przemyśle chemicznym są one wykorzystywane do produkcji rozpuszczalników, kwasów czy alkoholi o wysokiej czystości. Proces destylacji pozwala na skuteczne oddzielanie poszczególnych składników chemicznych oraz uzyskiwanie substancji o ściśle określonych parametrach jakościowych. W branży petrochemicznej destylatory odgrywają kluczową rolę w rafinacji ropy naftowej – dzięki nim możliwe jest uzyskiwanie paliw płynnych oraz innych produktów pochodnych ropy naftowej, takich jak oleje czy smary. W przemyśle spożywczym natomiast stosuje się je do produkcji napojów alkoholowych, takich jak whisky czy gin, gdzie precyzyjna kontrola procesu destylacji ma kluczowe znaczenie dla jakości finalnego produktu. Destylatory znajdują również zastosowanie w farmaceutyce do oczyszczania substancji czynnych oraz w przemyśle kosmetycznym do produkcji olejków eterycznych czy ekstraktów roślinnych.