Destylator przemysłowy
Destylator przemysłowy to urządzenie, które odgrywa kluczową rolę w procesach separacji cieczy na podstawie różnic w temperaturze wrzenia. W przemyśle chemicznym, petrochemicznym oraz spożywczym, destylacja jest niezbędnym procesem do uzyskiwania czystych substancji. Proces ten polega na podgrzewaniu mieszaniny cieczy, co prowadzi do parowania składników o niższej temperaturze wrzenia. Para następnie jest schładzana i kondensowana, co pozwala na oddzielenie jej od pozostałych składników. W przypadku destylatorów przemysłowych, wykorzystuje się różne technologie, takie jak destylacja frakcyjna czy destylacja próżniowa, aby zwiększyć efektywność procesu. Ważnym aspektem działania destylatora przemysłowego jest kontrola temperatury oraz ciśnienia, co pozwala na optymalizację wydajności i jakości uzyskiwanych produktów. W zależności od zastosowania, destylatory mogą być skonstruowane z różnych materiałów, takich jak stal nierdzewna czy szkło, co wpływa na ich trwałość i odporność na korozję.
Jakie są zastosowania destylatorów przemysłowych w różnych branżach
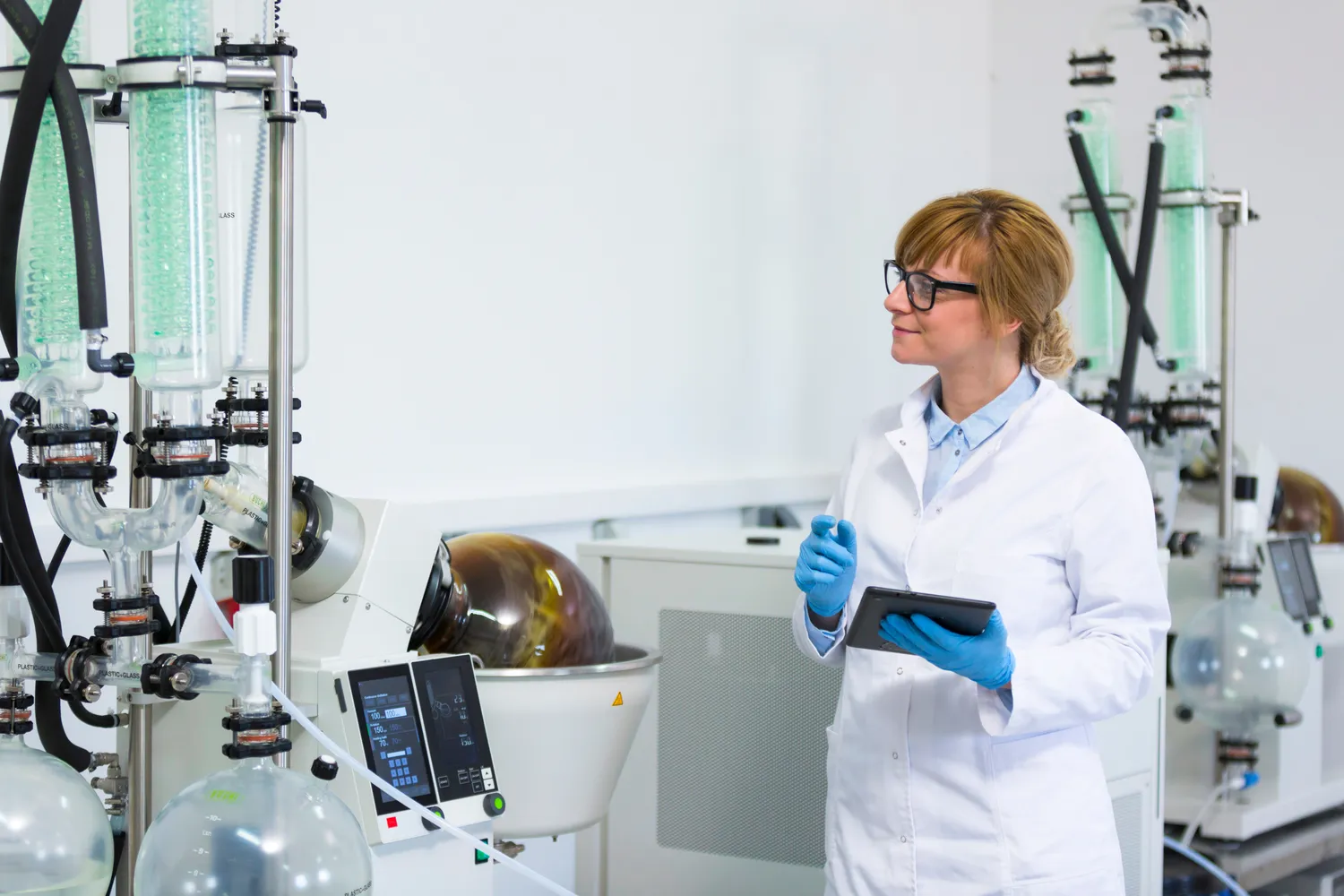
Destylatory przemysłowe mają szerokie zastosowanie w wielu branżach, co czyni je niezwykle wszechstronnymi urządzeniami. W przemyśle chemicznym są wykorzystywane do produkcji rozpuszczalników, kwasów oraz innych substancji chemicznych. Dzięki procesowi destylacji możliwe jest uzyskanie wysokiej czystości produktów, co jest kluczowe dla dalszych procesów produkcyjnych. W przemyśle petrochemicznym destylatory służą do separacji różnych frakcji ropy naftowej, takich jak benzyna, olej napędowy czy nafta. Każda z tych frakcji ma swoje specyficzne zastosowanie i wymaga odpowiednich parametrów procesu destylacji. W branży spożywczej destylatory są wykorzystywane do produkcji alkoholi oraz aromatów. Proces destylacji pozwala na uzyskanie wysokiej jakości trunków oraz ekstraktów smakowych, które są niezbędne w produkcji żywności i napojów. Ponadto, w ostatnich latach rośnie zainteresowanie ekologicznymi metodami produkcji, co prowadzi do rozwoju nowych technologii destylacyjnych, które minimalizują wpływ na środowisko naturalne.
Jakie są kluczowe elementy konstrukcyjne destylatora przemysłowego
Konstrukcja destylatora przemysłowego składa się z kilku kluczowych elementów, które mają istotny wpływ na jego wydajność oraz efektywność działania. Podstawowym komponentem jest zbiornik reakcyjny, w którym odbywa się proces podgrzewania cieczy. Zbiornik ten musi być wykonany z materiałów odpornych na wysoką temperaturę oraz korozję. Kolejnym ważnym elementem jest kolumna destylacyjna, która umożliwia separację składników poprzez wielokrotne parowanie i kondensację. Wysokość kolumny oraz jej średnica mają znaczenie dla efektywności procesu – im wyższa kolumna, tym lepsza separacja frakcji. Dodatkowo w konstrukcji destylatora znajdują się wymienniki ciepła oraz chłodnice, które pozwalają na skuteczne schładzanie pary i kondensację cieczy. Systemy automatyzacji oraz czujniki monitorujące parametry pracy również stanowią integralną część nowoczesnych destylatorów przemysłowych. Dzięki nim możliwe jest precyzyjne zarządzanie procesem oraz szybkie reagowanie na ewentualne nieprawidłowości.
Jakie są zalety stosowania nowoczesnych destylatorów przemysłowych
Nowoczesne destylatory przemysłowe oferują szereg zalet, które przyczyniają się do zwiększenia efektywności procesów produkcyjnych w różnych branżach. Przede wszystkim charakteryzują się one wysoką wydajnością energetyczną, co przekłada się na niższe koszty eksploatacji. Dzięki zastosowaniu zaawansowanych technologii automatyzacji możliwe jest optymalne zarządzanie procesem destylacji oraz minimalizacja strat surowców. Nowoczesne urządzenia często wyposażone są w systemy monitorujące jakość produktów końcowych, co pozwala na bieżąco kontrolować parametry procesu i dostosowywać je do zmieniających się warunków produkcji. Dodatkowo wiele nowoczesnych destylatorów projektowanych jest z myślą o ochronie środowiska – stosowane technologie pozwalają na redukcję emisji szkodliwych substancji oraz zużycia wody. Dzięki innowacyjnym rozwiązaniom konstrukcyjnym możliwe jest także łatwiejsze utrzymanie urządzeń w czystości oraz ich konserwacja.
Jakie są najczęstsze problemy z destylatorami przemysłowymi i ich rozwiązania
W trakcie eksploatacji destylatorów przemysłowych mogą występować różnorodne problemy, które wpływają na wydajność i jakość procesu destylacji. Jednym z najczęstszych problemów jest zatykanie kolumny destylacyjnej, co może prowadzić do obniżenia efektywności separacji składników. Zatykanie to często jest spowodowane osadzaniem się zanieczyszczeń lub nieodpowiednich substancji chemicznych. Aby temu zapobiec, ważne jest regularne czyszczenie kolumny oraz stosowanie filtrów przed wprowadzeniem surowców do destylatora. Innym problemem, który może wystąpić, jest niestabilność temperatury w zbiorniku reakcyjnym, co prowadzi do niejednorodności produktów końcowych. W takich przypadkach kluczowe jest monitorowanie parametrów pracy oraz dostosowywanie ustawień pieca grzewczego. Często zdarza się również, że proces destylacji nie osiąga oczekiwanej wydajności, co może być spowodowane niewłaściwym doborem materiałów lub konstrukcji urządzenia. W takich sytuacjach warto przeanalizować cały proces produkcyjny oraz skonsultować się z ekspertami, aby znaleźć optymalne rozwiązania.
Jakie są różnice między destylatorami przemysłowymi a laboratoryjnymi
Destylatory przemysłowe i laboratoryjne różnią się pod wieloma względami, co wynika z ich zastosowania oraz skali działania. Destylatory przemysłowe są projektowane z myślą o dużych ilościach surowców i wysokiej wydajności produkcji. Zazwyczaj mają one znacznie większe rozmiary i pojemności niż ich odpowiedniki laboratoryjne. W przemyśle kluczowe znaczenie ma efektywność energetyczna oraz ciągłość procesu, dlatego urządzenia te często wyposażone są w zaawansowane systemy automatyzacji i monitorowania. Z kolei destylatory laboratoryjne są zazwyczaj mniejsze i bardziej elastyczne, co pozwala na przeprowadzanie eksperymentów oraz testów na mniejszą skalę. W laboratoriach często korzysta się z prostszych konstrukcji, które umożliwiają łatwe dostosowanie do różnych warunków eksperymentalnych. Ponadto destylatory laboratoryjne często są wykorzystywane do uzyskiwania czystych substancji do badań naukowych, co wymaga precyzyjnego kontrolowania parametrów procesu.
Jakie innowacje technologiczne wpływają na rozwój destylatorów przemysłowych
W ostatnich latach obserwuje się dynamiczny rozwój technologii związanych z destylacją przemysłową, co ma istotny wpływ na efektywność i jakość procesów produkcyjnych. Jednym z kluczowych trendów jest wprowadzenie systemów automatyzacji oraz sztucznej inteligencji do zarządzania procesem destylacji. Dzięki tym technologiom możliwe jest optymalne dostosowywanie parametrów pracy w czasie rzeczywistym, co przekłada się na zwiększenie wydajności oraz redukcję kosztów operacyjnych. Kolejną innowacją są nowoczesne materiały konstrukcyjne, które charakteryzują się lepszą odpornością na wysoką temperaturę oraz korozję. Dzięki temu destylatory stają się bardziej trwałe i niezawodne w trudnych warunkach przemysłowych. Warto również zwrócić uwagę na rozwój technologii odzysku ciepła, które pozwalają na zmniejszenie zużycia energii poprzez ponowne wykorzystanie ciepła generowanego podczas procesu destylacji. Ponadto rośnie zainteresowanie ekologicznymi metodami produkcji, co prowadzi do opracowywania nowych technologii minimalizujących negatywny wpływ na środowisko naturalne.
Jakie są koszty inwestycji w destylatory przemysłowe
Koszty inwestycji w destylatory przemysłowe mogą być znaczne i zależą od wielu czynników, takich jak typ urządzenia, jego wydajność oraz zastosowane technologie. Przy zakupie nowego destylatora należy uwzględnić zarówno koszty zakupu samego urządzenia, jak i dodatkowe wydatki związane z instalacją oraz uruchomieniem systemu. Koszt zakupu może wynosić od kilku tysięcy do nawet milionów złotych w zależności od specyfiki projektu oraz wymagań klienta. Dodatkowo warto pamiętać o kosztach eksploatacyjnych, które obejmują zużycie energii elektrycznej, konserwację urządzenia oraz ewentualne naprawy. W przypadku dużych zakładów przemysłowych istotnym elementem jest także koszt przestrzeni potrzebnej do zainstalowania destylatora oraz związane z tym wydatki na infrastrukturę. Warto również rozważyć długoterminowe korzyści płynące z inwestycji w nowoczesne technologie – wyższa wydajność oraz niższe koszty operacyjne mogą przynieść znaczne oszczędności w dłuższym okresie czasu.
Jakie są przyszłe kierunki rozwoju technologii destylatorów przemysłowych
Przyszłość technologii destylatorów przemysłowych zapowiada się obiecująco dzięki ciągłemu postępowi technologicznemu oraz rosnącym wymaganiom rynku. Jednym z głównych kierunków rozwoju będzie dalsza automatyzacja procesów produkcyjnych, która pozwoli na jeszcze lepsze zarządzanie parametrami pracy urządzeń oraz zwiększenie efektywności energetycznej. Sztuczna inteligencja i uczenie maszynowe będą odgrywać coraz większą rolę w optymalizacji procesów destylacji poprzez analizę danych i przewidywanie ewentualnych problemów. Kolejnym istotnym trendem będzie rozwój ekologicznych technologii produkcji, które będą minimalizować negatywny wpływ na środowisko naturalne poprzez ograniczenie emisji szkodliwych substancji oraz zużycia zasobów naturalnych. Inwestycje w technologie odzysku ciepła oraz recyklingu substancji chemicznych staną się kluczowe dla branży chemicznej i petrochemicznej. Ponadto rosnące zainteresowanie biotechnologią może prowadzić do opracowywania nowych metod separacji składników opartych na procesach biologicznych zamiast tradycyjnych metod chemicznych.